Finishing Process
Hope's Power of 5™ Finishing System
Finishing processes for steel windows and doors vary dramatically from manufacturer to manufacturer. Hope’s takes tremendous pride in offering the ultimate finishing solutions geared to protect your investment whether your project is inland or ocean-front. Finishing processes must be carefully scrutinized to ensure products will perform, both aesthetically and functionally, for years to come.
To achieve the longest product life cycle. Hope’s employs the world’s most advanced finishing system. Developed in cooperation with top U.S. metallurgists and architectural coatings suppliers, Hope’s finishing system is engineered to ensure that windows and doors remain pristine and free from corrosion decade after decade, even in the harshest environments, inland or ocean-front.
Hope’s Power of 5™ Finishing System is the most comprehensive coating system available. For the top coat, there are unlimited color choices, including metallics and patinas. You can also work with Hope’s to create a custom color to perfectly integrate with your design.
COASTAL FINISHING PROCESS
Hope's Power of 5™ Coastal Finishing Process is specially designed to provide long-term protection against corrosion and abrasion for windows and doors within 1 mile of corrosive salt air environments.
Combined overall dry film thickness (DFT) shall be a minimum of 7.1mils.
INLAND FINISHING PROCESS
Hope's low-maintenance protective coating and finishing system provides incomparable long-term protection against corrosion and abrasion.
Combined overall dry film thickness (DFT) shall be a minimum of 4.6mils.
COASTAL FINISHING PROCESS
INLAND FINISHING PROCESS
COASTAL FINISHING PROCESS
COASTAL FINISHING PROCESS
Hope's Power of 5™ Coastal Finishing Process is specially designed to provide long-term protection against corrosion and abrasion for windows and doors within 1 mile of corrosive salt air environments.
Combined overall dry film thickness (DFT) shall be a minimum of 7.1mils.
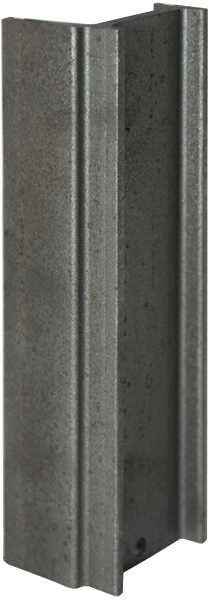
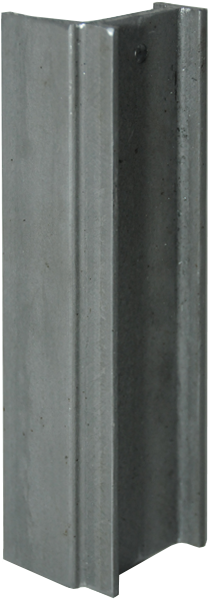
1 CLEANING
2 HOT-DIP GALVANIZING
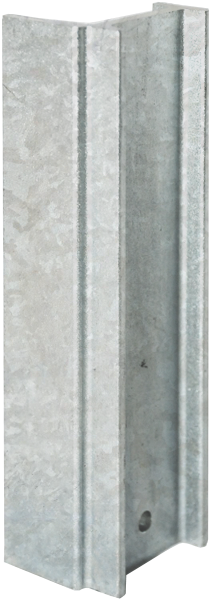
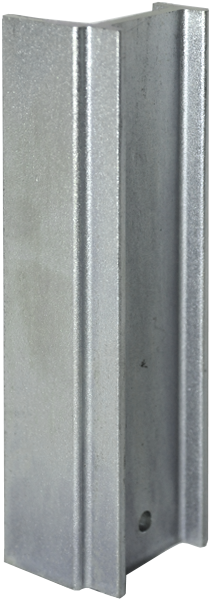
3 BRUSH-OFF BLAST CLEANING
- All hot-dip galvanized parts shall be brush-off blast cleaned in accordance with SSPS-SP16 to profile surface prior to primer application.
- All parts shall be oven-heated prior to finishing to prevent out-gassing through epoxy primer.
4 EPOXY POWDER PRIMER
- Within 12 hours of hot-dip galvanizing pretreatment all frames and accessories shall receive an epoxy powder primer.
- Epoxy powder primer is applied electrostatically to a dry film thickness (DFT) of 2.0-4.0mils and oven cure in preparation of top coat application.
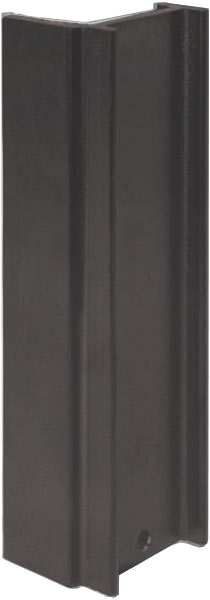

5 FINAL TOP COAT
The final top coat is your selection to establish the desired color and aesthetic of the finished product. Hope's offers various coatings including acrylic polyurethane or polyester powder top coats. Both coatings have options for custom color matching, different sheens, metallic flakes, and artistic/weathered finishes.
Click the link below to download our standard Paint Color Palette.
Contact your Hope's representative to determine the best finish option for your project.
COASTAL FINISHING PROCESS
INLAND FINISHING PROCESS
Hope's low-maintenance protective coating and finishing system provides incomparable long-term protection against corrosion and abrasion.
Combined overall dry film thickness (DFT) shall be a minimum of 4.6mils.
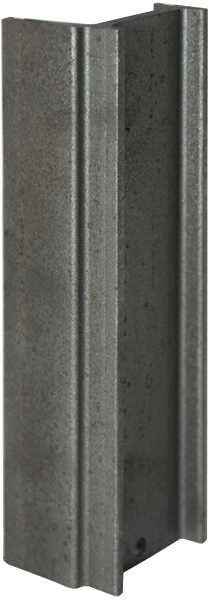
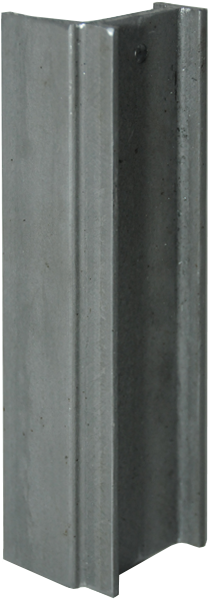
1 CLEANING
2 PRETREATMENT
Following all machining and welding operations, all solid hot-rolled steel windows and doors shall receive a thorough 12-stage pretreatment process.
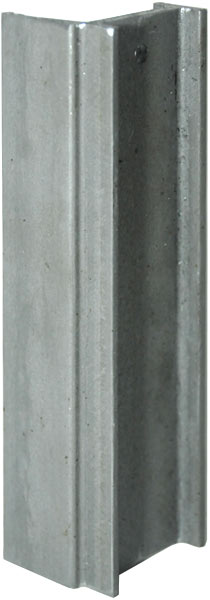
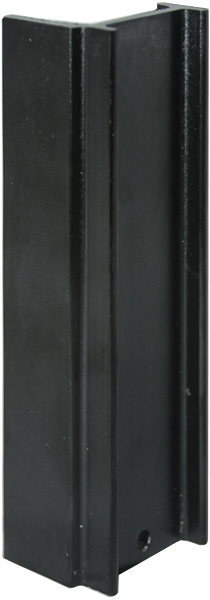
3 EPOXY E-COAT PRIMER
4 EPOXY POWDER PRIMER
Following pretreatment and e-coat primer, all steel parts shall receive an abrasion resistant epoxy powder coat compliant to ISO 12944-6 C5-M.
- Powder is applied electrostatically over cured E-caot toa dry film thickness (CFT) of 2.0-3.0mils.
- Parts are oven-baked at 325° to completely cure prior to final top coat.
- Powder coat is intended as an intermediate finish applied prior to the final finish top coat.
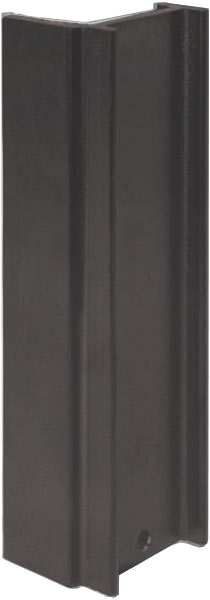

5 FINAL TOP COAT
The top coat defines the final stage to the overall aesthetics and performance of the finished product. Hope's ultraurethane polyurethane finish is a blend that offers outstanding UV stability, superior touch-up capability, low chalking and fading characteristics, unlimited color matching, and 70,000+ standard colors, including metallics.
Click the link below to download our standard Paint Color Palette.
Contact your Hope's representative to determine the best finish option for your project.
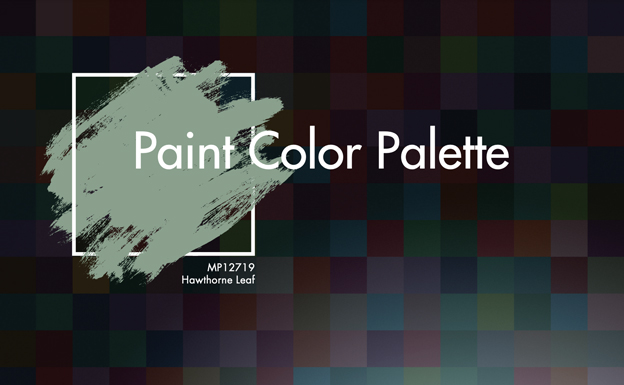
STANDARD PAINT COLOR PALETTE
Color chip samples are as close as possible to actual colors within the limitation of RGB digital on-screen reproduction.
POWER OF 5 PERFORMANCE
Overall process shall provide full documented compliance with the following criteria:
- SSPC-SP8 for acid pickling
- ASTM D714-02 Paint Blistering Test
- ASTM D4585 Humidity
- ASTM D1654-05 painted Products in Corrosive Environment
- ASTM B117-03 Salt Spray (Fog) Test
- ASTM G85 Cyclic Fog/Dry Test (Prohesion)
- ASTM D5894-96 Salt Fog/UV Painted Metal
- ASTM D4541 Pull Off Strength of Coating Test